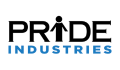
CalcuQuote’s Cloud-Based Platform Transforms PRIDE Industries’ Quoting Process
PRIDE Industries, a social enterprise dedicated to creating employment opportunities for people with disabilities, partnered with CalcuQuote to modernize and streamline its manual and time-intensive quoting process, achieving a 40% reduction in turnaround times and significantly improving efficiency and customer satisfaction. By consolidating workflows into CalcuQuote’s cloud-based platform with automated tools and enhanced data tracking, PRIDE Industries streamlined operations and gained valuable supply chain insights.
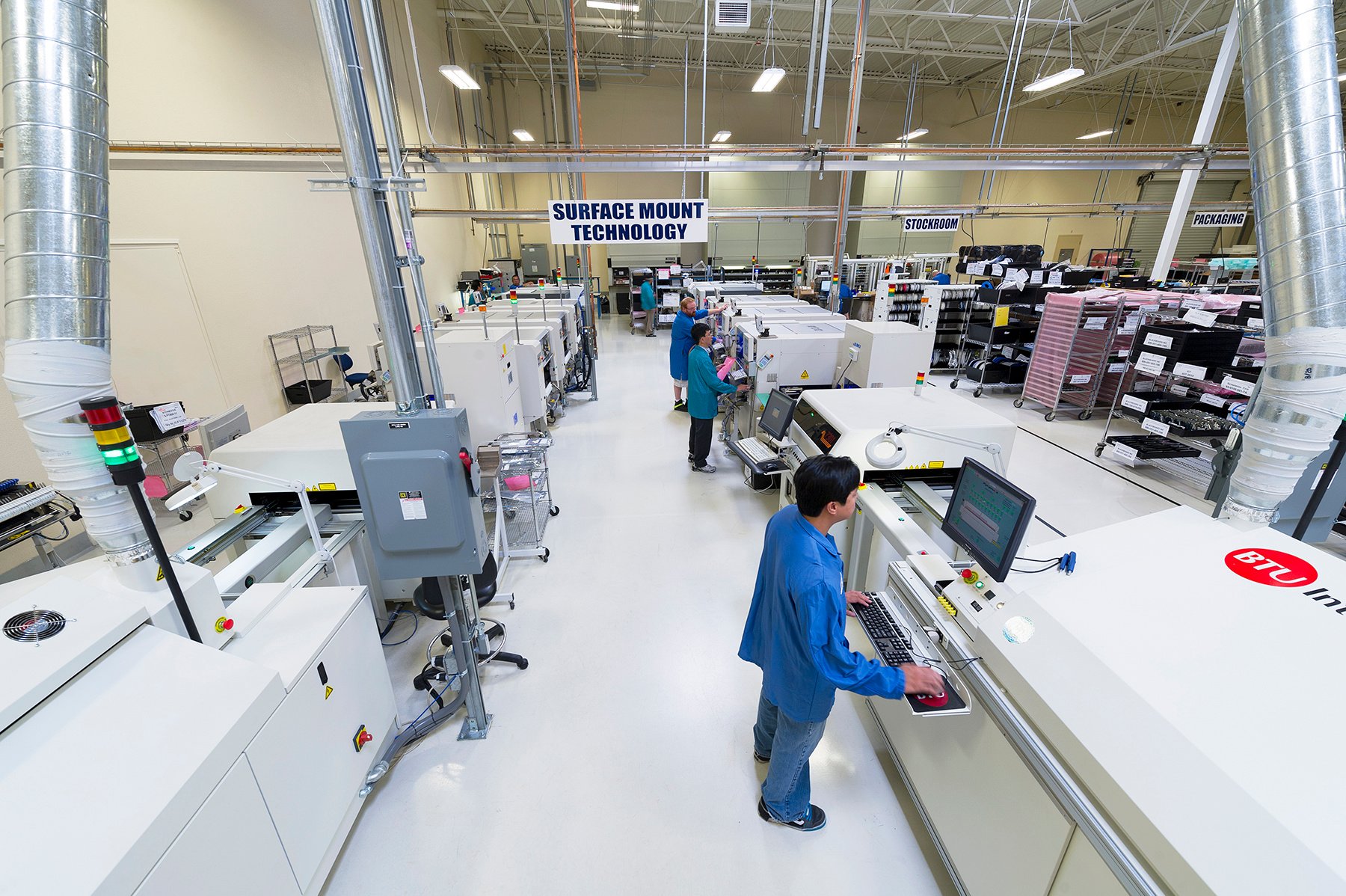
About PRIDE Industries
Company size
Customer
Products in use
Location
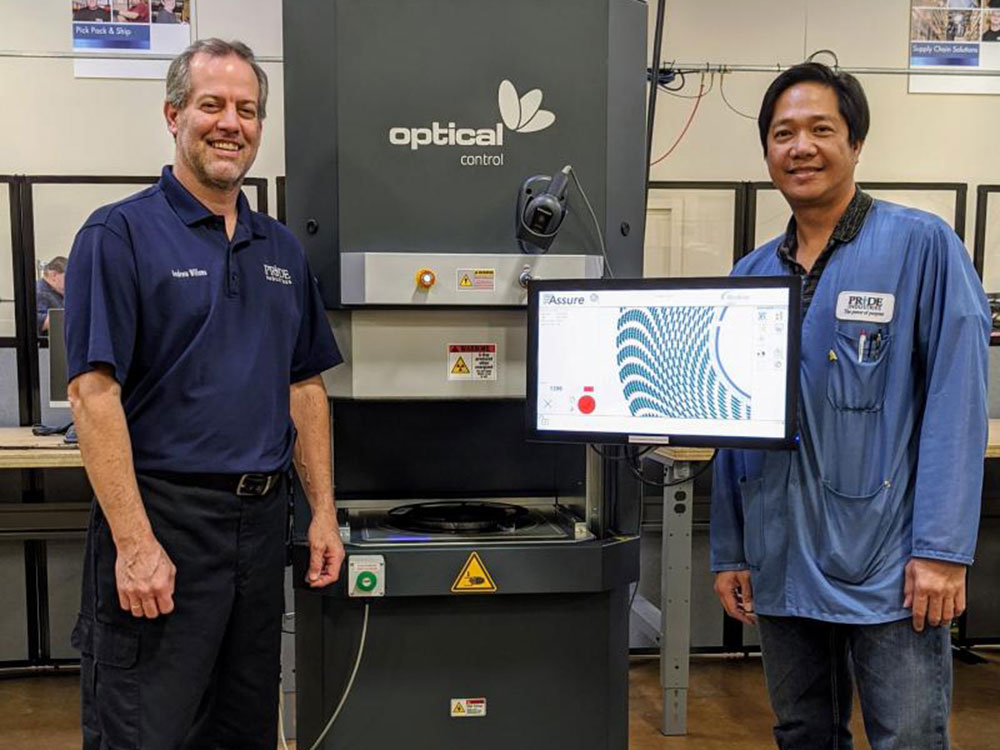
“Partnering with CalcuQuote has revolutionized our quoting process. What once required the use of four separate tools—two spreadsheets, an in-house system, and a cloud platform—has been streamlined into a single, efficient cloud- based solution. This transformation slashed our quote turnaround time by an impressive 40%, enabling us to respond to opportunities faster than ever before.”

Challenges
Before adopting CalcuQuote, PRIDE Industries faced the following challenges:
- Manual Quoting Processes: Quotes were managed through spreadsheets, emails, and
network-based files. Procurement and labor quoting relied heavily on manual effort, making
the process time-consuming and error-prone. - Inefficiency: Averaging 3-8 hours per quote, the process required input from 4-8
employees, consuming 60-80 hours per week. Turnaround times ranged from 12-15 days
for turnkey quotes and 4-6 days for consigned quotes. - Disconnected Systems: The company relied on four separate systems for quoting, creating inconsistencies and making it difficult to compare past quotes or leverage data for repricing.
- Limited Visibility: Metrics like win/loss ratios, costs, and turnaround times were tracked manually, restricting insights into process performance. Also, there was no data available to easily leverage customer reprice efforts.
- Supply Chain Disruptions: Addressing part challenges and material pricing relied on manual
procurement and engineering efforts, causing delays and inefficiencies. - Complexity of Custom Quotes: Although the quoting process was fairly detailed and partially documented, it was inefficient for complex or custom products, significantly slowing the process and reducing overall efficiency.
- Customer Feedback: Slow quote turnaround times negatively impacted customer satisfaction and limited PRIDE Industries’ ability to add new business.
Objective
- Improve consistency and accuracy in quotes.
- Reduce quote turnaround times to align with industry standards.
- Streamline processes into a unified, end-to-end solution.
- Enhance data tracking and analytics for actionable insights.
- Support scalability without requiring additional personnel resources.
Solution and implementation
PRIDE Industries implemented CalcuQuote’s cloud-based platform, which offered:
- Streamlined Workflows: Migrating from four systems to a single, unified platform.
- Automation via APIs: Simplified material pricing and MPN resolution, reducing procurement effort and avoiding delays while also decreasing the turnaround time for quotes. Since much of what was quoted was new, MPN challenges became a fully manual process with Procurement and Engineering, adding days to the quoting process.
- High-Volume Quoting Flexibility: The ability to quote high volumes for material cost savings
while applying labor costing tailored to smaller build lot sizes. This provided PRIDE Industries with the flexibility to offer multiple quote options to customers within a single proposal. - User-Friendly Interface: A clean and intuitive web-based interface that enabled multiple teams (sales, procurement, account management, and engineering) to collaborate seamlessly.
- Comprehensive Features: Support for labor rate calculations, alternate material suggestions, checklist builders, and revision tracking ensured consistent and complete quotes while also allowing history changes to be tracked within a single quote, avoiding the need to create new quotes for revisions.
- Enhanced Support: CalcuQuote’s responsive customer service team provided onboarding
assistance and ongoing support to address any configuration challenges.
Results
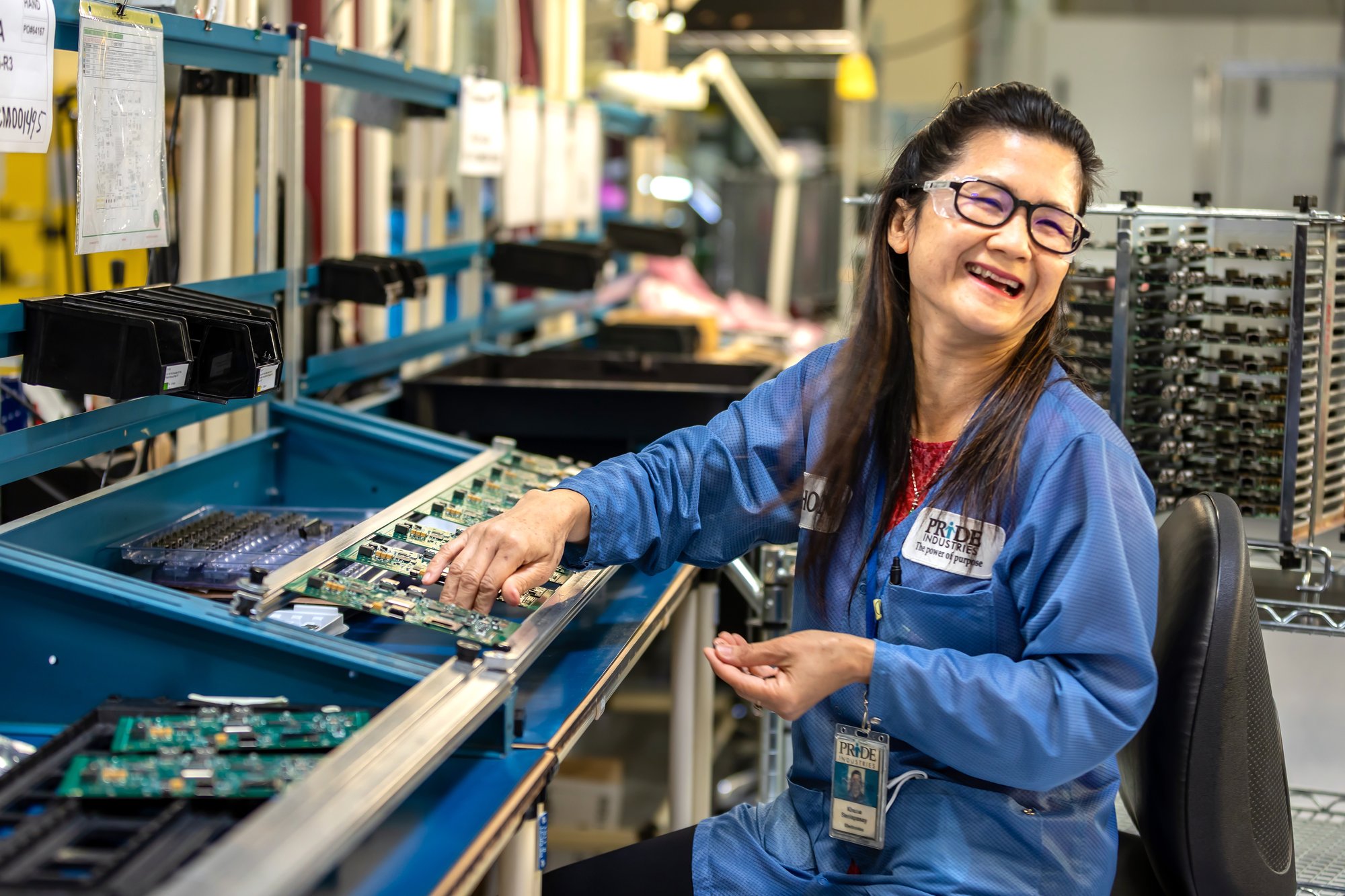
improvements for PRIDE Industries:
- Turnaround Time: Average turnaround times were reduced by 40%, dropping to 6-8 days for turnkey quotes and 1-2 days for consigned quotes.
- Efficiency Gains: Streamlined workflows decreased manual effort, freeing up employee time for other tasks. Additionally, the implementation of CalcuQuote eliminated the need to create a full-time role for quote management. With the system in place, the process is now managed by a large group of people, each with a small portion of the process.
- Customer Satisfaction: Faster and more consistent quotes received positive feedback from customers, enhancing PRIDE Industries’ competitiveness.
- Improved Data Utilization: Metrics such as win/loss ratios, costs, and potential revenue were tracked seamlessly within the system, supporting strategic decisions.
- Simplified Repricing: Efforts for entire product families became more manageable, enabling quicker and more accurate updates for existing business.
- Enhanced Quote Management: Multi-assembly quotes, previously complex to manage, were now handled efficiently. The ability to track revision changes and maintain history for quotes streamlined processes further, while flexible quoting capabilities supported both high-volume material cost savings and labor costing for smaller build lot sizes.
- Supply Chain Insights: Early visibility into part challenges allowed PRIDE Industries to provide quotes with alternate suggestions, helping customers resolve issues before placing orders.
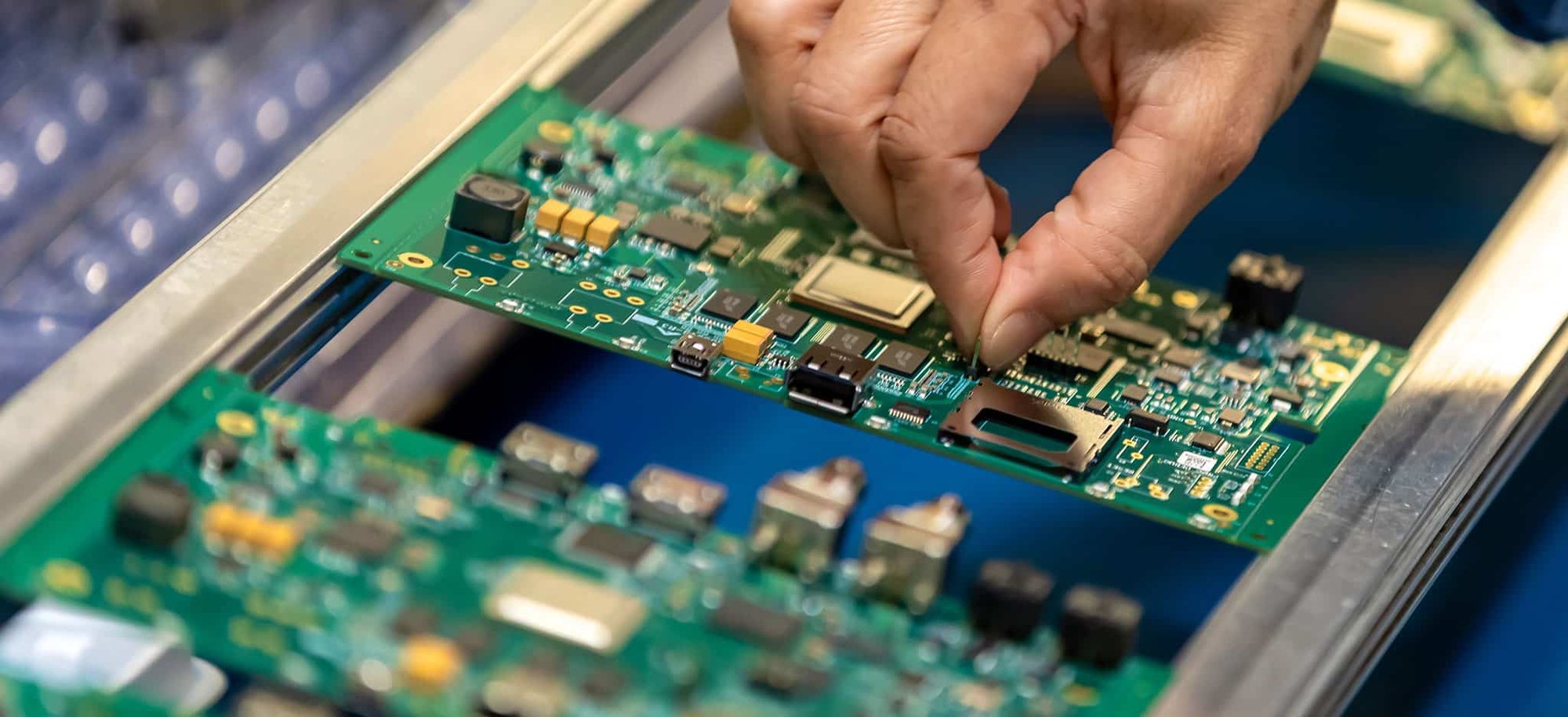
Future plans
PRIDE Industries aims to deepen its integration of CalcuQuote with its ERP system to enable seamless data sharing and enhanced automation. Additionally, the company plans to explore new features such as dynamic workflow editing, improved quote cloning, and expanded high-volume quoting capabilities.
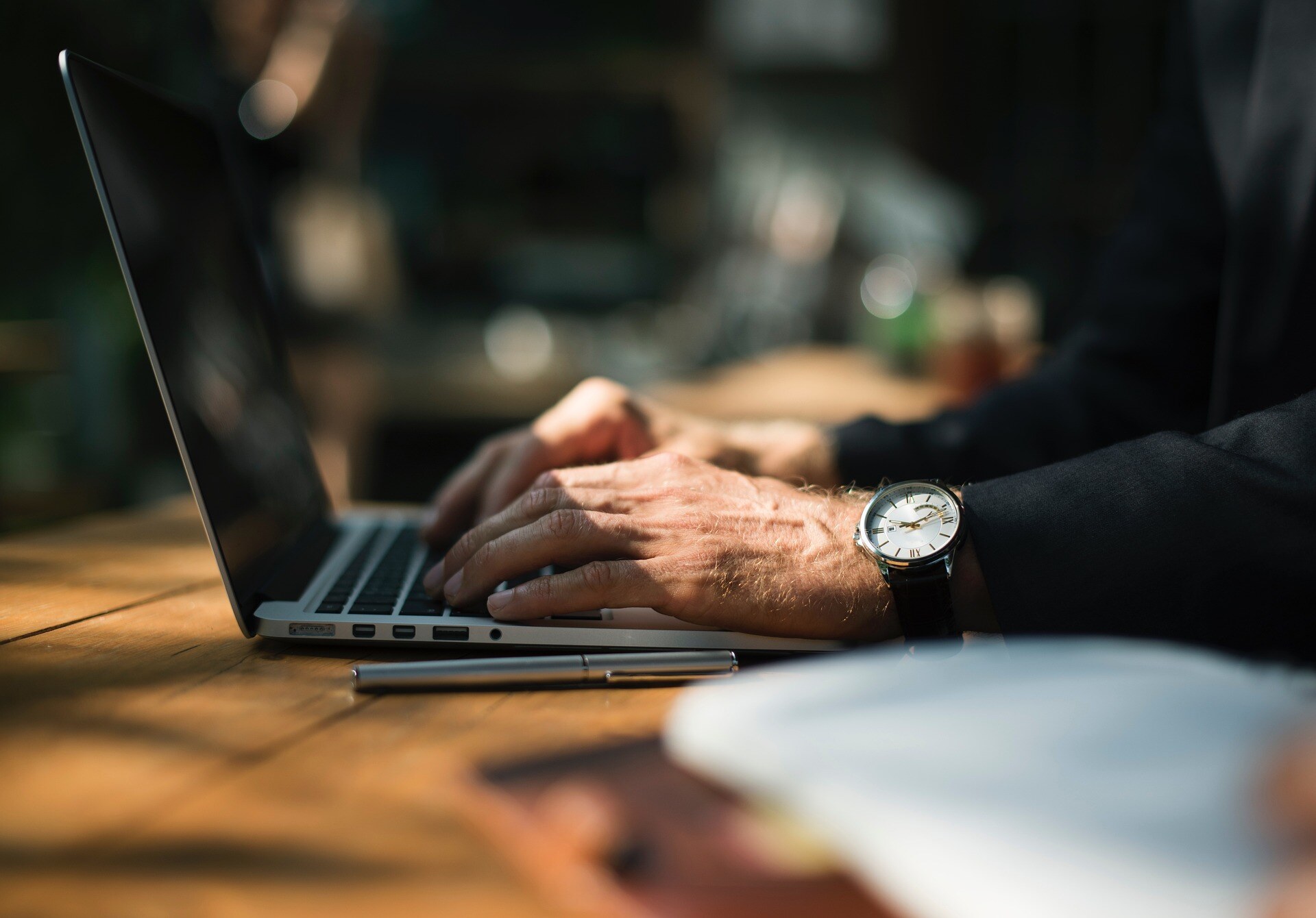
Interested in the same success?
We have 10+ years of EMS experience. We are happy to offer you a free demo and help you achieve your business goals.